In the underwater world, noise can be a sentence. The more silent a submersible, the lower the probability that it is detected by sounding. Although artificial intelligence begins to change the rules of the gameefforts to further reduce the acoustic firm do not cease. As SCMP points outthe last advance arrives from China, where a team of researchers has developed a technology that, in laboratory conditions, has managed to significantly cut the vibration that is transmitted from the engine to the helmet.
The idea starts from replacing the traditional engine rigid supports with a hybrid structure of active-peasive insulation. The system was presented at A study reviewed by pairs published in Noise and vibration control By researchers from Jiao Tong University in Shanghai, in collaboration with China State Shipbuilding Corporation (CSSC). According to the authors themselves, a reduction of only 10 decibels at the noise level of a underwater vehicle could decrease its 32%detection range.
A double control system. The system combines two elements. On the one hand, a steel-gum-steel ring that acts as a passive shock absorber. On the other, a series of 12 piezoelectric actuators that surround the engine and neutralize micromovimientos with the help of precision levers. These actuators are designed to adapt to reduced assembly space. The combination allows to reduce both structural vibrations and low frequency sounds, the most problematic for stealth.
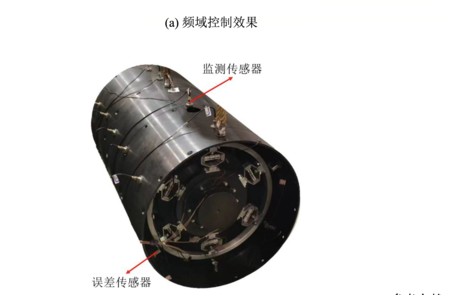
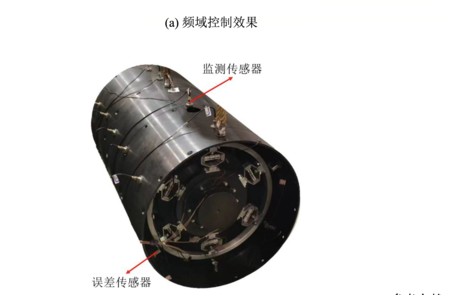
The system is governed by an FX-LMS algorithm, an adaptive method that coordinates the 12 actuators and avoids interference between them. Thanks to this intelligent management, the system can adjust your response in real time, which allows you to maintain control even in the face of unexpected variations in engine behavior. The method is based on rebuilding the interfering signal to feed the noise cancellation.
Promising results, but in laboratory. The tests were performed with a 200 kg simulated engine mounted on a cylindrical metal housing. The system was designed to operate with a regime of 1,500 revolutions per minute (25 Hz). At 100 Hz, the passive system managed to reduce noise by 12 dB. With the complete system, the attenuation reached 24 dB. At 400 Hz, the reduction was 26 dB. The researchers explain that the chosen frequencies correspond to the most common spectral lines of the engine.
A development still with questions. The study also indicates limitations. The rigidity of the rubber used in the passive system can be affected by temperature and pressure variations, and the durability of piezoelectric actuators has not yet been verified in real operating conditions. In addition, researchers do not specify what type of underwater would use this technology or the final impact that it would have on its global acoustic profile. In fact, the term “underwater vehicle” is used throughout the study.
That is, they do not speak of diesel-electrical submarines or nuclear submarines. For now, it is an experimental development with promising results. The participation of CSSC suggests strategic interest, but there is no confirmation that this system has been integrated into any operational platform. What demonstrates is that China continues to bet on advanced technologies to reinforce its underwater stealth, an important factor in the modern naval war.
Images | TOOK-RANCH (Wikimedia Commons) | Jiao Tong University
In Xataka | The war in Ukraine had a red line of 70 kilometers. West has just eliminated it after Russia’s last attack
GIPHY App Key not set. Please check settings